手机壳手板CNC加工工艺分析 本文关键字 手机壳,手板,分析
(4)注意要先铣出基准截面,以免翻转装夹时胚料(半成品)调错方向。
(5)注意先要模拟切削,检查无误,才后置处理,进入数控加工。
二、制作过程
(2)手机壳的壁厚只有1.5mm,加工外表面时易变形,破碎,需要在已加工好的型腔中填入填充物作为支撑(本例采用的是石膏作为填充物)。应避免先加工出通孔部位(显示屏、按键孔),再填充石膏,否则很难分离成品和填充物。
(3)先恢复修剪的曲面,遮盖住手机壳手板的表面通孔位置,进行整面加工,再挖槽完成通孔加工。以免加工到通孔部位加工时刀路起伏不畅顺,切削力不均匀,造成过切、塌角、崩角,成品受损。
2.1 手板次加工—手板变腔
2.1.1图形处理
根据胚料尺寸构建毛坯平面,并画出基准边框,设有基准截角(6×45°);进入NC,建立一个新的加王坐标系M—MODE;以坐标原点为中心,在ZX平面180°翻转整个图形,严禁用镜像命令;用此时手机上盖更面的内轮廓线修剪毛坯面,露出手机上盖的所有内表面;
画出毛坯底面与侧面;x、y轴加工原点要与图形中心重合,以此时手机上盖的更面为Z轴原点。图形如图3所示。
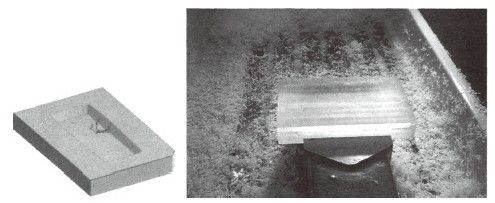
图3建立加工坐标系 图4切削毛胚
2.1.2工件装夹
用平口钳夹紧胚料,露出至少16mm,长宽与计算机图形一致,如图4所示。X、Y简单分中,胚料更面降lmm为Z轴原点,进行对刀。
2.1.3编程加工
(1)程序shuojill(用直径为10mm的端铣刀D10),分别用走刀方式POCKET(挖槽加工)精加工更面,参数如下:刀具转速为1500f/min、下刀量每刀1mm、进给速度800mm/min,铣削范围为Z=1mm至Z=0,铣去多余材料;用走刀方式WCUT(环绕等高)粗加工型腔,参数如下:刀具转速为1500r/min、下刀量每刀1mm、进给速度1200mm/min、留0.4mm余量,加王到腔底;再用走刀方式PROFILE(外形铣切)精加工基准,参数如下:刀具转速为1500r/min、下刀量每刀1mm、进给速度800mm/min,加工至Z=-10mm。加工结果如图5所示。
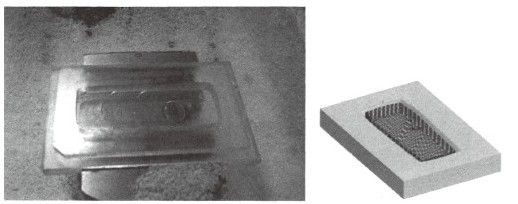
图5 粗加工实物图 图6 半精加工刀路图
(3)程序shuojil3(用直径为4mm的端铣刀D4)工件型腔底部与周边更小圆角仅R0.5mm,更好直接用端铣刀精加工。若用球刀精加上,型腔底部小圆角不能加工到位,还需要端铣刀清角,两把刀精加工容易造成刀路接痕,影响表面质量,而且效率不高,所以这里直接采用D4端铣刀精加工;用走刀方式WCUT(用精加工加补刀方式)精加王型腔,参数如下:刀具转速为2 500r/min、下刀量每刀0.25mm、补刀刀距为0.3mm、进给速度1200mm/min,加工到腔底;再用PROFILE(外形铣切)把手机壳装配部位加工出来,参数如下:刀具转速为2500r/min、下刀量每刀0.2mm、进给速度500mm/min,加工深度为1mm,正前方向圆弧进刀;加工实物如图7所示。
(2)程序shuojil2(用直径为6mm的端铣刀D6)由于工件内腔四周更小圆角R1.5mm,粗加工(刀具半径5mm)加工不到,残留余量较大。需要先清角,再精加工,否则精加工到此处时受力突然加大,易振动过切甚至断刀。用走刀方式WCUT(用精加工加补刀方式)半精加工型腔,参数如下:刀具转速为1800r/min、下刀量每0.5mm、补刀刀距为1mm、进给速度1 200mm/min、留0.3mm余量,加工到腔底;刀路如图6所示。
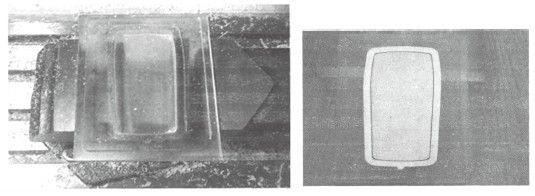
图7 半精加工实物图 图8 填充石膏
2.2 填充石膏
用适量的石膏粉与水一次性勾兑,不了太稀;拆下工件清洁,将石膏浆倒入已加工好的型腔中;待干硬后,用平口尺刮平面,如图8所示
2.3手板第二次加工—加工手板外表面及按钮荧幕位置
2.3.1图形处理
进入NC,建立一个新的加工坐标系Z、X、Y轴加工原点要与图形中心重合,以工件的地面为Z轴原点(因底面是已加工面)
2.3.2
装夹工件

图9 反面加工定位 图10 反面加工实物图
手动铣去部分的多余边,让基准边外露,方便使用分中棒;清洁机床工作台面与工件,注意去除油污;将工件平放在机床工作台面上,注意基准截角位置要与电脑图形一致;用百分表校直基准边(确保两次加工基准重合);在工件周边适量滴入胶水。风干后,用分中棒找正X、Y轴原点;Z轴以机床工作台面为原点。装夹好的工件如图9所示。
2.3.3 编程加工
(1)程序shuoji21(用直径为6mm的端铣刀D6)考虑到用大刀具受力过大振动容易造成工件松动,小刀刚性太小而容易造成断刀,故使用D6端铣刀;用走刀方式WCUT(环绕等高)粗加工工件,参数如下:刀具转速为1800r/min,下刀量每刀1mm,进给速度800mm/min、留0.4mm余量,加工至Z=2.5mm。
(3)程序shuoji23(用直径为3mm的端铣刀D3)由于手机壳按键的更小圆角为R1.5mm,而且侧壁底部精加工不能受力过大,故采用D3平底刀。先用走刀方式SRFPRF(曲面投影加工)精加工显示屏、按键孔,由于手机上盖的壁厚有1.5mm,故先要将外表面向内补正(OFFSET)2.5mm做出辅助曲面用来投影,以确保铣穿石膏。
(2)程序shuoji22(用半径为3mm的球刀R3)球头刀加工曲面可以更好的保证加工表面质量,故使用R3的球刀;用走刀方式WCUT(用精加工加补刀方式)精加工工件外表面,参数如下:刀具转速为2500r/min、下刀量每刀为0.3mm、补刀刀距为0.2mm、进给速度1200mm/min,加工至Z=2.5mm。加工实物如图10所示。
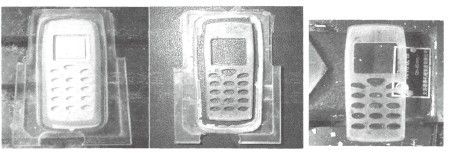
图11 完成手板加工 图12 手板成型
方法送行对刃时,所调用的刀具不受顺序的限制,在加工过程中可随时调用其它的刀具,其误差也较小,而采用相对方法对刀时,调用刀具必须以标准的刀具进行对刀,然后再调用其它的刀具,如果采用配以仪器对刀也比较方便,但是采用试切法时有时不易使两把刀具重合,容易引起误差。对于单把刀具进行对刀时可直接采用相对对刀试切法,不用进行各刀偏参数的设置,这可大大地提高加工效率。
参数如下:刀具转速为3000r/min,下刀量每刀0.3mm,进给速度800mm/min、加工2.5mm深。再用走刀方式WCUT(环绕等高)精加工工件侧面,参数如下:刀具转速为3000r/min、下刀量每刀为0.3mm、进给速度1200mm/min、加工至Z=1.5mm(由于手机壳配合位高度为1mm,不能完全切断成品与胚料,要留0.5mm余量连接,防止加工到更后成品脱落受援)。加工实物图如图11所示。
2.4手工成形
将小木棍伸入机床工作台T形槽内,小心用力撬起工件;清洁机床,可用小刀刮去胶水残迹;小心分离成品与残余胚料;小心敲击石膏,分离成品与石膏;用小锉刀修平成品外表周边。如图12所示。
三、刀偏的设定在加工中的应用
在加工过程中,如果能够正确的利用刀偏值的设置与子程序的调用,可以有效地缩短编程时间,提高加工效率,加工如图l所示的零件,在制订好加工工艺后,如果采用单步循环的方法,每次粗车4mm时,可进行如下的编辑,大概用近30条指令:
01234
Nol G92x35 Z15
N02 G00 Z O
N03 GOl X-2 F200 M03 M04
N04 X24
N05 G02 Z-18 R4
N06 Gol X35
N07 G00 ZO
..........
N20 G0l X-l
N21 X10 C2
N22 G02 Z-18 R4
N23 G01 X35
N24 G00 ZO
N25 M30
如果采用刀补值的形式进行编程加工,假定使用的刀具为1号刀,可在刀偏表不同的刀偏号中设定不同的值,然后选用Ol刀补号为标准值,再设定02、03...刀补号的X方向的偏值值分别设定为4,4,...,2,进行调用刀补号即可;
0002
T010l
N01 G92X35 Z15
M98 P0003
...
M30
0003
N04 X24
N05 G02 Z-18 R4
N06 G01 X35
N07 G00 Z0
M99
这只是为刀偏的使用提供了一种思路,具体的使用还随着不同的方法进行改变。
四、总结
手板制作不仅在新产品开发中得到广泛应用,而且还可用于设计验证,产品评估,生产过程分析,检验,制造工具的制作等,大大缩短生产准备时间,明显地改善公司的竞争能力。CNC手板以其率、高精度和高表面质量为基本特征磊受到用户的欢迎,目前的高速加工中心已经可以用直径为0.3mm刀具进行加工,随着CNC机床的不断发展,以及CNC雕刻机的使用,CNC手板将会在手板制作方面得到广泛应用。
对于手动对刀的数控车削加工中,刀偏的正确设定及对刀方法的准确,对零件的加工质量有着决定性的作用,这对广大的数控爱好者尤其是初学者是非常重要的一个环节,只有掌握了这种方法,才能进行进一步的学习与操作。
手机壳手板CNC加工工艺分析,欢迎咨询合作。